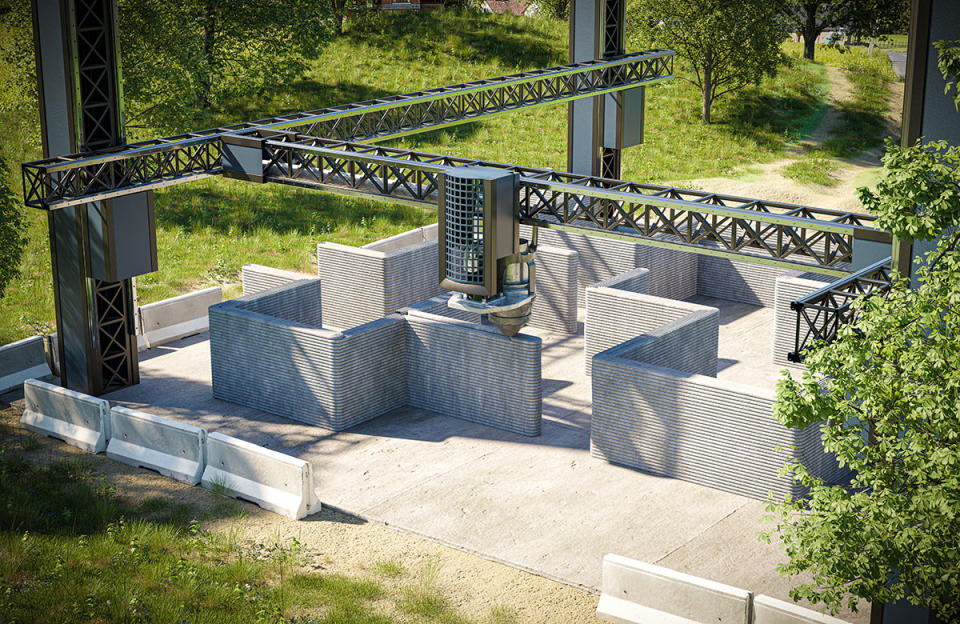
Adhering To a $600,000 research study give to the city of Nome, Alaska, that was released in 2015, elderly authorities at the U.S. Department of Housing and Urban Development (HUD) saw the College of Alaska at Fairbanks to promote the opportunities that 3D printing innovation might give the building of budget friendly real estate in the united state
The give mosted likely to a job group including companions at Penn State College and a not-for-profit research study company, the Xtreme Habitats Institute (XHI). The companions will certainly perform the “layout, design, products research study, growth, preparation, and evaluation” that is needed for 3D printing of “premium, budget friendly, energy-efficient, and lasting real estate for areas in sub-arctic areas of Alaska,” HUD explained.
HUD gives and connected job
Pupils at Penn State will certainly function to “improve, examination and layout methods” for the mobile printing device at the heart of the initiative that will certainly be relocated to the city of Nome. There, the group will certainly make use of a specialized 3D printer “created and constructed for the setting to construct and examine a model home,” HUD clarified.
A vital objective for the task consists of the implementation of regional and lasting sources for building products. Past HUD, the college and the city of Nome, various other companions consist of the Alaska Real Estate Money Corp., the Cold Environment Real Estate Proving Ground, the National Renewable Resource Lab, XHab 3D Inc. and Fairbanks Products Inc.
Today, HUD authorities– consisting of Solomon Eco-friendly, major replacement aide secretary (PERSONAL ORGANIZERS) for plan growth and research study; Richard Monocchio, Personal organizers for public and Indian real estate; and Northwest local manager Andrew Lofton— showcased this brand-new innovation at an occasion.
” We require to assume larger, bolder, and extra artistically than ever before if we wish to develop the affordable homes of the future,” Greene stated in a declaration. “Below at HUD, we are utilizing cutting-edge remedies to develop the real estate our expanding country requirements. This 3D printer is an interesting depiction of this brand-new frontier, and we can not wait to see it at the office.”
Lofton stated the presentation noted a “memorable day,” including that using brand-new and unique innovations might have a large influence on widespread real estate supply problems– which are improving— throughout the country. This is specifically real for locations with severe environments like Alaska.
” Today, we showcased the most up to date instance of just how technical technology, when coupled with regional expertise and solid neighborhood collaborations, can assist us develop the high quality, budget friendly, and resistant homes our nation requires,” Lofton stated.
Price and performance capacity
Previously this year, an article in Smithsonian Publication took a better check out the capacity for 3D-printed homes. The chance exists, the short article clarified, as the rate of the innovation outmatches conventional approaches and expenses are starting to drop.
Sierra Romas, a recipient of a Habitat for Humanity home in Newport Information, Virginia– that was profiled in the short article– explained the experience of viewing a 3D printer style 166 different concrete layers that would certainly create the wall surfaces of her home as “unique.”
” Concrete printing is much faster– the wall surfaces for Sierra’s 1,300-square-foot home were created in around 40 hours,” the short article mentioned. “It’s likewise ending up being more affordable than standard wood-frame structure, which has actually altered bit in a century.”
The Environment for Mankind Peninsula and Greater Williamsburg phase in Virginia has actually created 3 3D-printed homes in Virginia up until now, with even more heading. The company’s chief executive officer stated that the expense has actually reduced with each succeeding task.
” Sierra’s expense Environment regarding $215,000, which totaled up to $25,000 much less than the very first one; the land was without the city’s real estate authority,” the short article mentioned.
The short article included that building is cleaner and the homes are extra power reliable considering that concrete is much better for insulation. They are likewise much less most likely to refute or be blown down, which might be attractive for insurers.
3D printers utilized for these jobs likewise need just one or 2 individuals to run, which might be an essential information as the country faces a shortage of construction workers, according to info launched in January by Connected Contractors and Specialists
Economical real estate building using 3D printing has also taken place in Texas, where a set of start-ups look for to place a damage in stock and address environment adjustment problems by utilizing 3D printing innovation to develop homes in main sections of the state.